Japanese Sword Materials
How "Tama-hagane" is made
1. Iron Sand Sorting.

Using a magnet, the iron sand is separated from
regular sand.
Too litlle sand will make it difficult to drain the slag.
Too much sand will produce too much slag.
Therefore, even the very first step is critical to determine the quality of the steel.
2. Preparing the Furnace Base.

The base of the Tatara furnace is coated with clay.
The clay used on the furnace is sorted beforehand and is different to the clay used for forging.
The base is prepared each time, depending on the amount of Iron Sand and Charcoal that is to be used.
Since this stage is integral to the quality of the Tamahagane steel, the clay is carefully and accurately applied.
3. Drying in a Tatara furnace.
![IMG_3617[1].JPG](https://static.wixstatic.com/media/84e9aa_732cfb1dd0824519a66fe64791f90b84~mv2.jpg/v1/crop/x_189,y_284,w_3843,h_2657/fill/w_366,h_253,al_c,q_80,usm_0.66_1.00_0.01,enc_auto/IMG_3617%5B1%5D_JPG.jpg)
The furnace is then assembled and left to dry for over a week
(Even when short on time, it must dry for at least 3 days)
Proper drying is important because leftover moisture can disturb the melting process.
4.Charcoal Cutting.
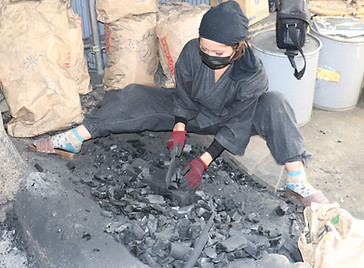
Charcoal to be used in the furnace is cut into smaller pieces.
A lot of charcoal is required, so around 60-70kg is cut and prepared.
Because so much is needed, we will continue to cut the charcoal at the same time as the smelting progresses.
The furnace heats up while more charcoal
5.Heating the Furnace.

Charcoal and kindling are used to fuel to fire.
As the temperature of the furnace rises, any remaining moisture is evaporated.
Once the furnace is heated, we begin to add iron sand. Timing is very important though and the inside of the furnace must be constantly monitored.
6.Adding Charcoal & Iron Sand.

Once the coal levels out, iron sand is poured into the top of the furnace.
After that, we alternate between adding coal and iron sand, every 5 minutes.
This continues whilst monitoring the inside of the furnace carefully and adjusting the quantities accordingly.
7.Draining the Iron Slag.
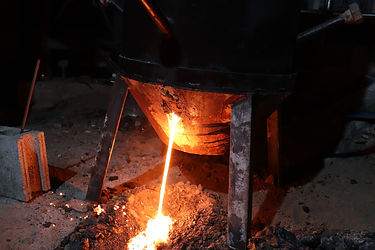
remove the throat before the loom (impurity) approaches the feather mouth.
the back is too little or too much, so i pull it out while watching the steelmaking situation.
it prevents the throat from entering between the rolled ball steel in moderation.
(This is also repeating many times during the smelting process)
8.Tatara Furnace Dismantling.
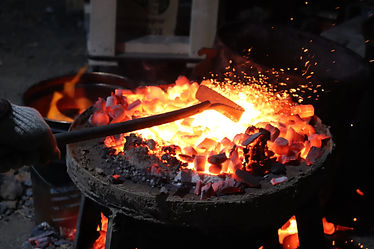
Steps 4, 6 & 7 are repeated continuously for around 8-9 hours. The furnace is then dismantled.
※The time can vary depending on the amount of iron sand※
The top section of the furnace is removed first, and then the middle section.
9.Steel Collection.


The block of steel is removed from the furnace.
It’s difficult to temper in its current state, the block is first cut into quarters and cooled in cold water.
That is the end of the process to make the Tamahagane required for Japanese blades.
Generally between 8-11kg of Tamahagane can be collected at one time.
It takes roughly 1kg to produce a standard kitchen knife.